The first set of drives to be replaced were the Fan Pump drives. Four drives each rated at 1,500 HP and supplied with 480V 3-phase at 2,000 Amps per drive. In all, 16 drives would be replaced with a total connected horsepower of just under 10,000.
Paper machine drive upgraded with minimal downtime
When a paper plant began experiencing a growing number of failures and difficulty finding spare parts for the drive system on a critical paper machine, they sought a solution to begin replacing the 20-year-old GE Siltron drives with new ABB DCS800 digital drives. After comparing proposals from a number of integrators, Applied Motion Systems was selected to provide an engineered solution that would allow them to remain in production while replacing their drives section by section during regularly scheduled, short duration maintenance downtimes. This approach required a retrofit solution that lent itself to fast deployment into existing drive enclosures while taking advantage of the existing power distribution infrastructure.
Assessing the existing installation
The original paper machine drives were located in an MCC room in dedicated OEM cabinets over an open cable way in the concrete floor. This cable way provided access to, and passage for motor and feedback cables routed to and from the paper machine.
A number of details made this far from a drop-in replacement. First, while the ABB drives were narrower and shorter than their GE counterparts, they were also significantly deeper. This required fabrication of new enclosure doors that would provide the needed clearance to the front of the drive when the door was closed. Also, the entry point for drive power, as well as the point where the motor leads exited the drive were located differently on new and old drives. These differences along with several others created a number of challenges when considering integration of the ABB drives into the legacy GE cabinets.
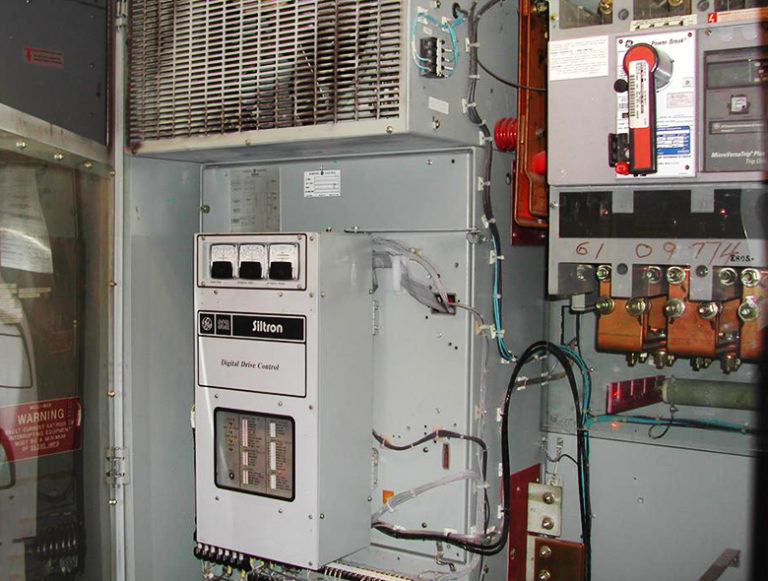
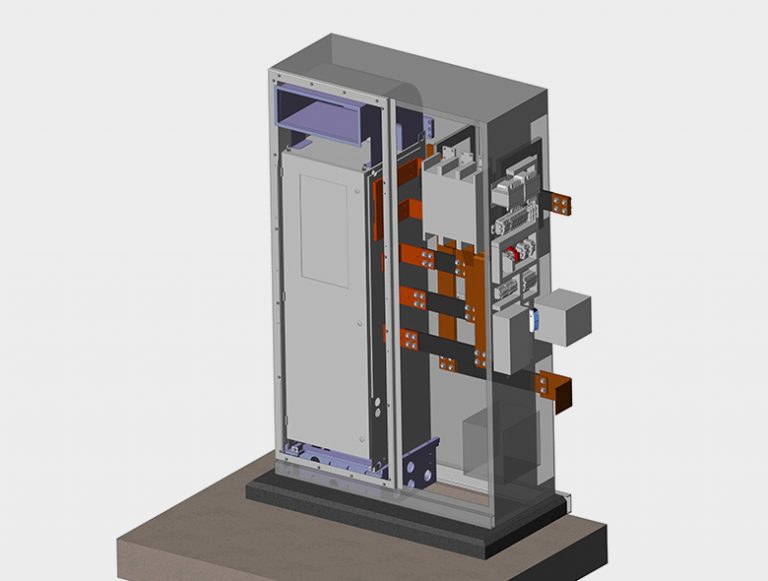
A measure-up was conducted to gather information about the existing drive cabinets, power distribution arrangement, and motor lead conductors. This information was used to create a CAD model of the existing installation from which a retrofit kit could be designed that would facilitate quick removal and replacement of the legacy GE drives.
Facilitating an efficient upgrade
AMS developed a solution for each challenge encountered in order to bring about a fast, efficient, and safe drive retrofit. First, the drives being removed from the cabinets weighed in excess of 800 pounds and made for a potentially unsafe rigging and unloading operation in the constrained space of the MCC room. Also, given the significant differences in location of power and armature lead locations on the ABB drives compared to the GE drives, AMS designed and manufactured a Flexibus-based solution that would simplify routing of power to the new drives. Finally, the drive mounting arrangements and ventilation configurations varied greatly between new and old drives and required a unique solution for each drive frame size.
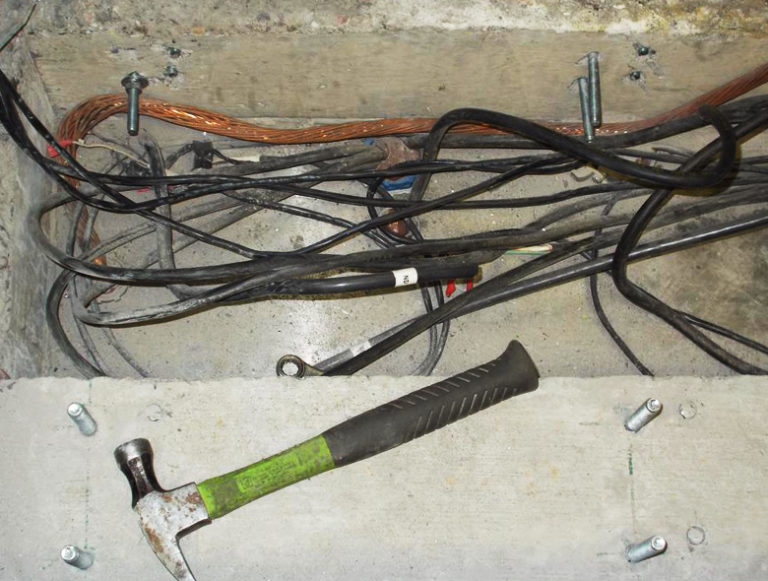
For the largest frame size drives, AMS designed an offset lifting fixture that allowed use of an overhead hoist to safely lift each drive out of its enclosure. Once the drive was out of the enclosure, the concrete enclosure floor and cable way trench were clearly visible.
The replacement ABB drives weighed 700 pounds and were designed for a sliding base / bolted bracket mount.
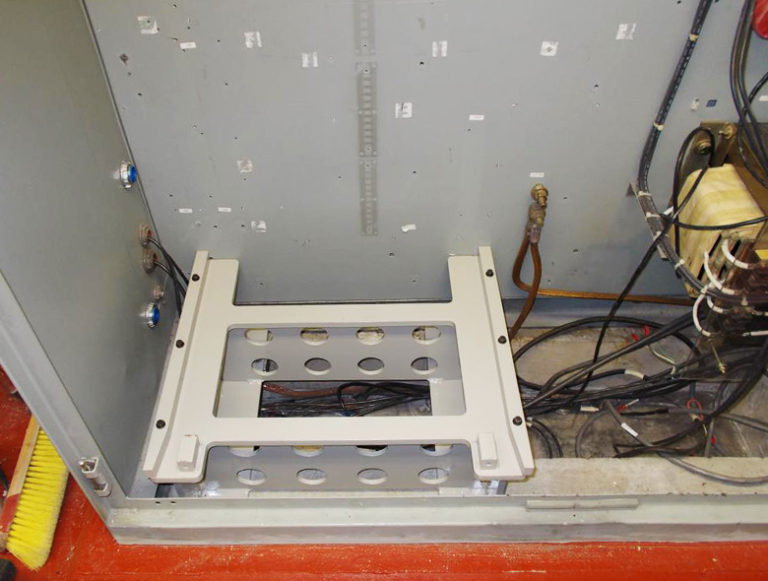
The existing enclosures lacked the structural integrity for this mounting arrangement so AMS designed a lower support bracket that would span the cable way and anchor to the concrete below the enclosure. This bracket would support the weight of the drive while additionally providing a means to safely and easily slide the new drive module into the cabinet. Once in place, the ABB base mounting flange bolted directly to the AMS designed floor bracket.
AMS also designed and manufactured an upper mount that would bridge the gap between the top rear surface of the drive and the enclosure. This bracket included an integral AMS designed air plenum that served to direct heated air from the drive cooling fans to the new enclosure door to exhaust into the climate controlled MCC room.
Routing power to the new drives
The next priority was to navigate the process of delivering as much as 2,000 Amps to the new drives from the existing power bus infrastructure. AMS mechanical engineers modeled the existing power bus structure and then designed a Flexibus interface between the existing bus and new fusing, line reactor, and drive power input lugs.
A copper bussing kit comprised of precision formed and drilled bussing and fasteners was provided to allow simplified installation. Black plastic insulated sleeves protect laminated Flexibus sections that prevent stresses from vibration from damaging the drive or disconnect.
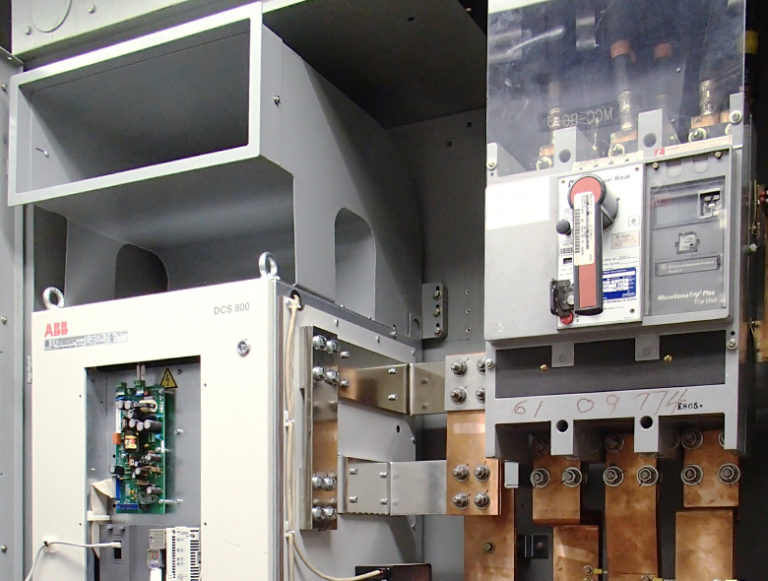
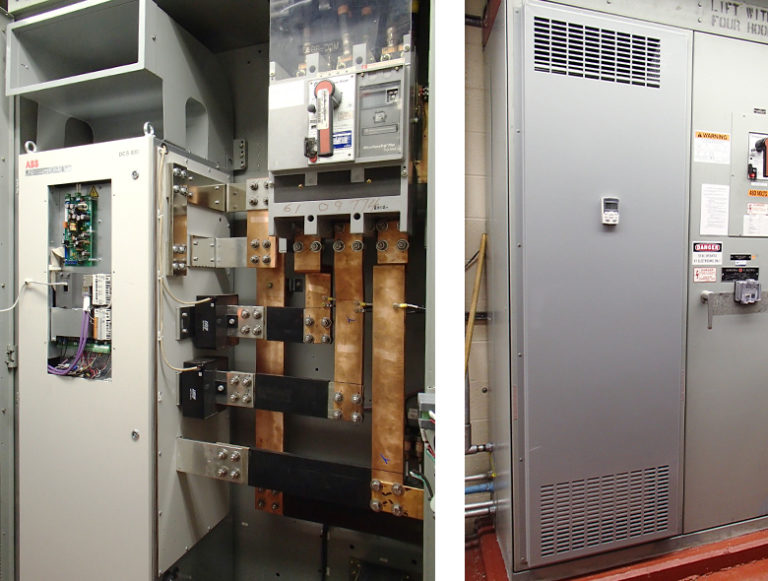
A roadmap for a fast and efficient startup
Every effort was made to perform as much work as possible before arriving on site in an effort to facilitate a safe, efficient, and timely installation and commissioning of the drives. A detailed commissioning guide was created for each installation phase. This guide provided clear direction for not only what hardware to remove with the original GE drive, but also what hardware to retain. Likewise, the sequence of installation of the new ABB drive provided clear direction at each step avoiding common missteps. Key details pertaining to the order of installation, correct fastener usage, and required torque settings eliminated second guessing and reduced the potential for rework. Once the physical installation was complete, a clear set of instructions and checks guided engineers through remaining tasks to get the drives properly configured, powered up, and commissioned.
When it was time to bring the new drives to life, this step by step guide led our team through each task, from confirming jumper settings, to armature and field current loop tuning, to verifying motor position feedback and direction and then final tuning under load.
Workspace files, which are organized parameter lists that are useful for quickly viewing a specific group of drive parameters were prepared beforehand using ABB’s drive software. These pre-defined workspace files streamlined each step of the drive commissioning process by allowing engineers to focus attention on relevant parameters associated with the task at hand.
Our partners on the customer side were extremely satisfied to see our team complete the installation and commissioning of all 16 drives within the 4 schedule down times – and even more so as they began to experience the updated system’s benefits: significant energy savings due to optimized field voltages and much improved paper machine performance from improved sectionalized drive coordination from the wet end to the winder.
start the conversation
All of our collaborations begin with an open dialogue.
Get in touch with us using this simple form, and a member of our team will follow up with you soon.