Deploying a Class IV laser within a Class I system means rethinking many common machine design elements because the hazardous laser energy must be enclosed within a light-tight container. This should be as easy as mounting the laser equipment to the inside of a metal box, right? Though this may sound simple, it can be quite challenging to implement this solution while juggling other requirements such as part presentation, air ventilation, and maintainability. Here are some creative ways engineers at AMS have overcome these obstacles.
Laser Integration
Laser technology can be found everywhere in modern manufacturing in both additive and subtractive processes, from the smallest sensors to the largest machine tools. Common uses include cleaning, marking, texturing, cutting, drilling, welding, and 3D printing. As a systems integrator and machine builder, Applied Motion Systems has invested significant time and resources into deploying this versatile technology in ways that simplify its use for customers while abiding by all applicable regulations and standards.
Integrating lasers into automation solutions can present a wide range of engineering challenges spanning multiple disciplines, including mechanical, electrical, and control system elements. At a basic level, engineers must consider things like laser physics, applications recipes, environmental cleanliness, and thermodynamic behavior. At a much higher level, they must navigate a complex landscape of standards and government regulations due to the potential safety hazards posed to humans.
Regulations and standards
At the Federal level, laser products and their implementation fall under the governance of the U.S. Food and Drug Administration Center for Devices and Radiological Health (FDA-CDRH). All regulations are documented in the Code of Federal Regulations (CFR), Title 21, Subchapter J “Radiological Health”, including all definitions, procedures, and requirements. Additional state and local regulations may also apply. Major non-regulatory standards concerning lasers include International Electrotechnical Commission (IEC) standard 60825-1 and American National Standards Institute (ANSI) standard Z136.1. Many other organizations have further standards and guidelines to address the use of lasers in more particular contexts: OSHA, NFPA, FAA, ACGIH, and ICNIRP just to name a few*. Clearly, the integration of lasers into various types of machinery requires both specific administrative knowledge as well as engineering expertise in order to maintain proper compliance and functional safety.
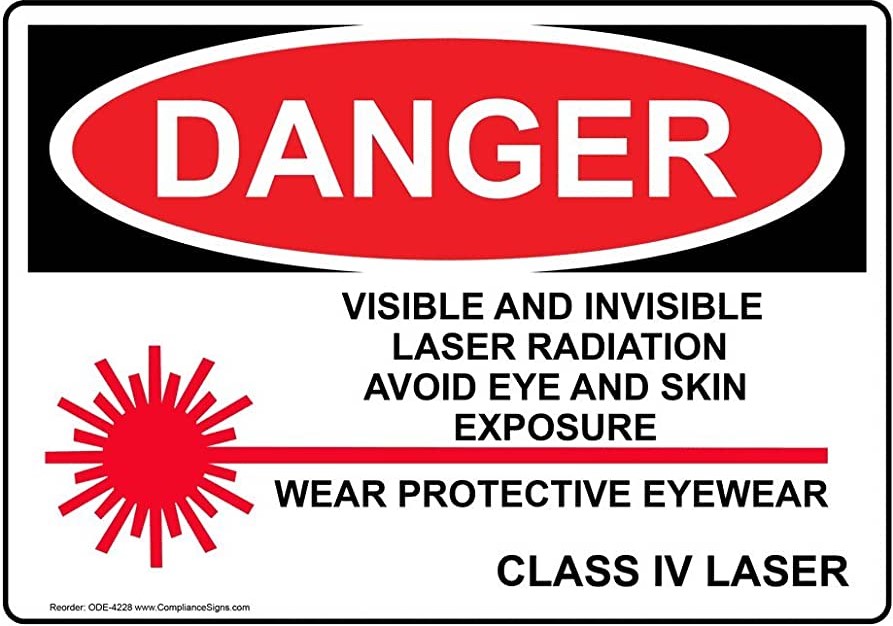
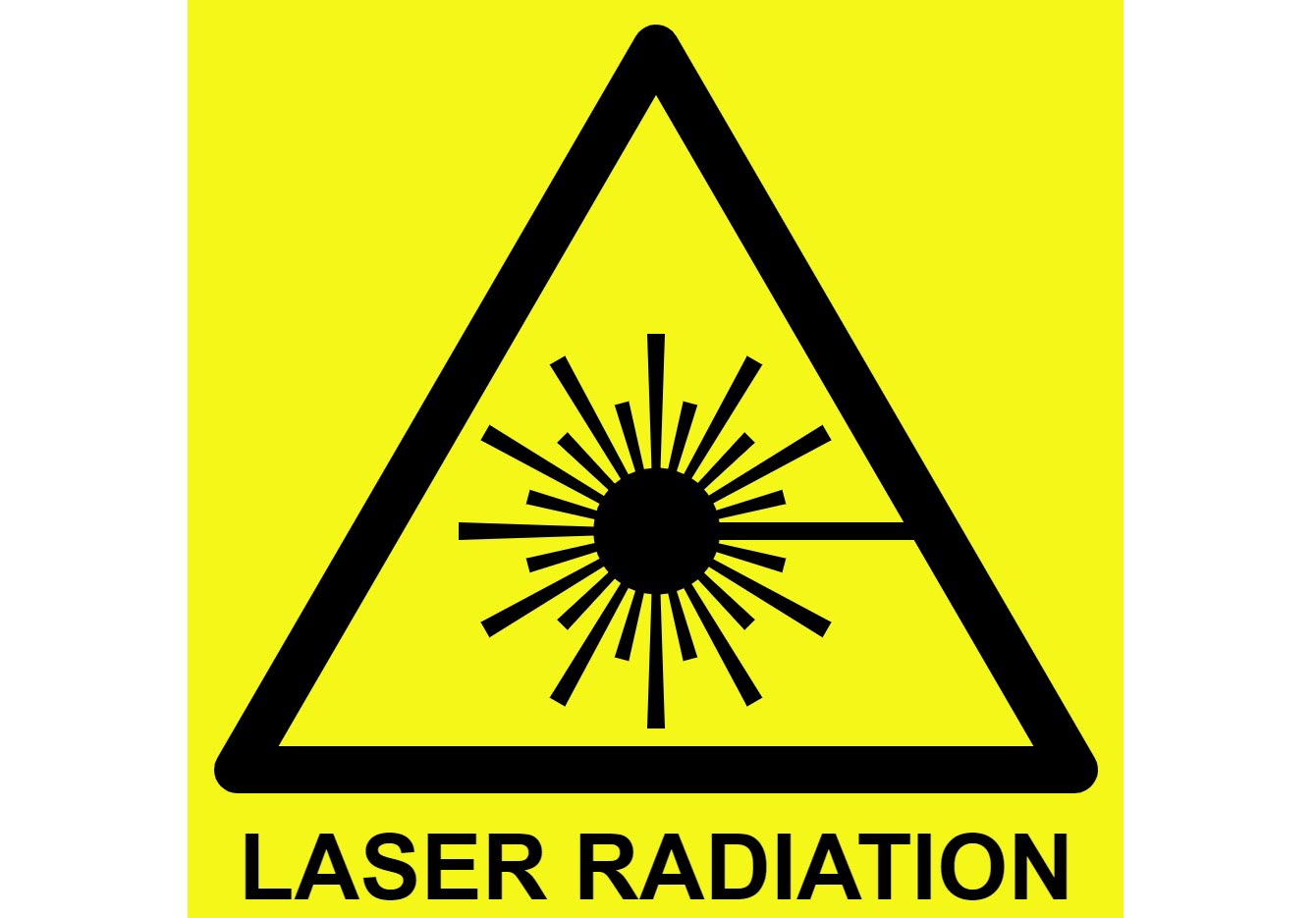
The classification system of laser products as defined in 21 CFR Part 1040 forms the basis for laser regulations. The FDA-CDRH recognizes four classes of lasers based on a quantity called the Accessible Emission Level (AEL) – the maximum amount of laser light (direct or scattered) to which a human may be exposed during operation of the product. Class I lasers are completely safe to operate without any protective equipment because of sufficiently low AEL or an enclosure that isolates harmful laser light (e.g. Lidar devices, CD player). Class II lasers and above are considered hazardous to varying degrees, Class IV being the most dangerous, causing severe damage to human eyes and tissue in just fractions of a second.
Reclassification
Most lasers used in industrial applications are Class IV, so how can they be implemented safely and effectively? Fortunately, this is familiar territory for AMS, having deployed several Class IV lasers in automated machinery. The key is that users of Class IV laser products are permitted to reclassify their devices as Class I laser products if the laser is deployed in accordance with established criteria (e.g. ANSI Z136). Since a laser’s class depends on the AEL, a system designed to block all light from escaping during operation can be recertified and reclassified in compliance with FDA-CDRH regulations. AMS has achieved this in a variety of applications – including laser welding and laser marking – so that our customers may enjoy the benefits of enhanced safety, operability, and efficiency.
Designing with lasers
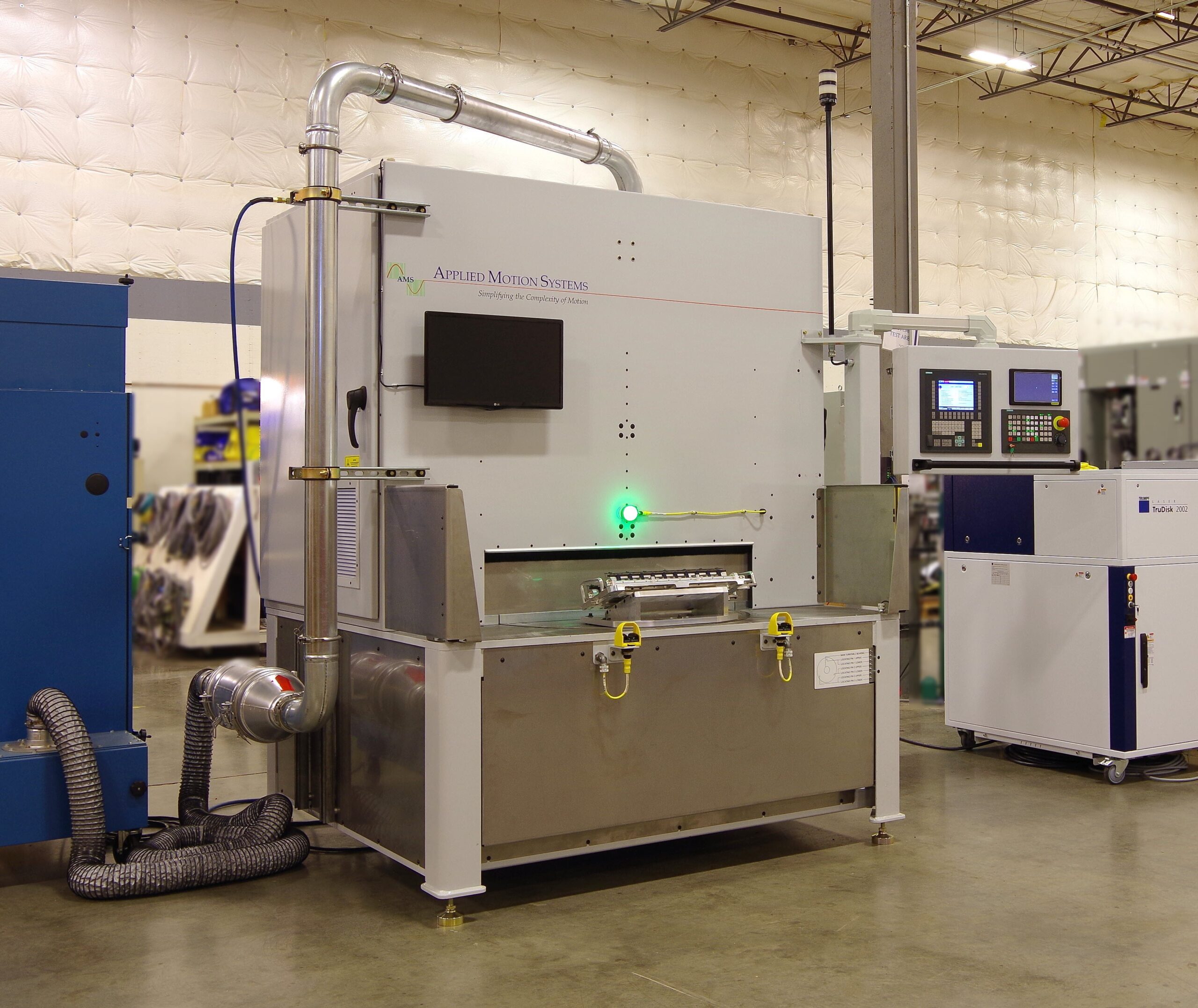
Part Presentation
In industrial laser applications such as welding and marking, parts must be introduced into the laser enclosure for processing and then removed post-processing, requiring both a door to access the enclosure and a mechanism to transfer the parts. Access points used for part presentation during operation of the machine are controlled by the machine itself, typically using pneumatic actuators. Per FDA-CDRH requirements, access points to the enclosure must be monitored by safety interlocks that inhibit laser output while they are open.
To transfer parts in and out of the laser enclosure, AMS has deployed a variety of solutions. For example, a turntable style design allows parts to be loaded and unloaded on one side of the table – outside the machine’s enclosure – while welding operations are performed on the opposite side of the table – inside the machine’s enclosure. The enclosure door operates in conjunction with the table, opening to rotate parts and closing to seal and safely operate the laser. Another excellent solution is to employ a robot to pick and place parts to be processed, reaching into the enclosure through the access door. While keeping operators safe from hazardous laser energy, these designs maximize repeatability and throughput for customers.
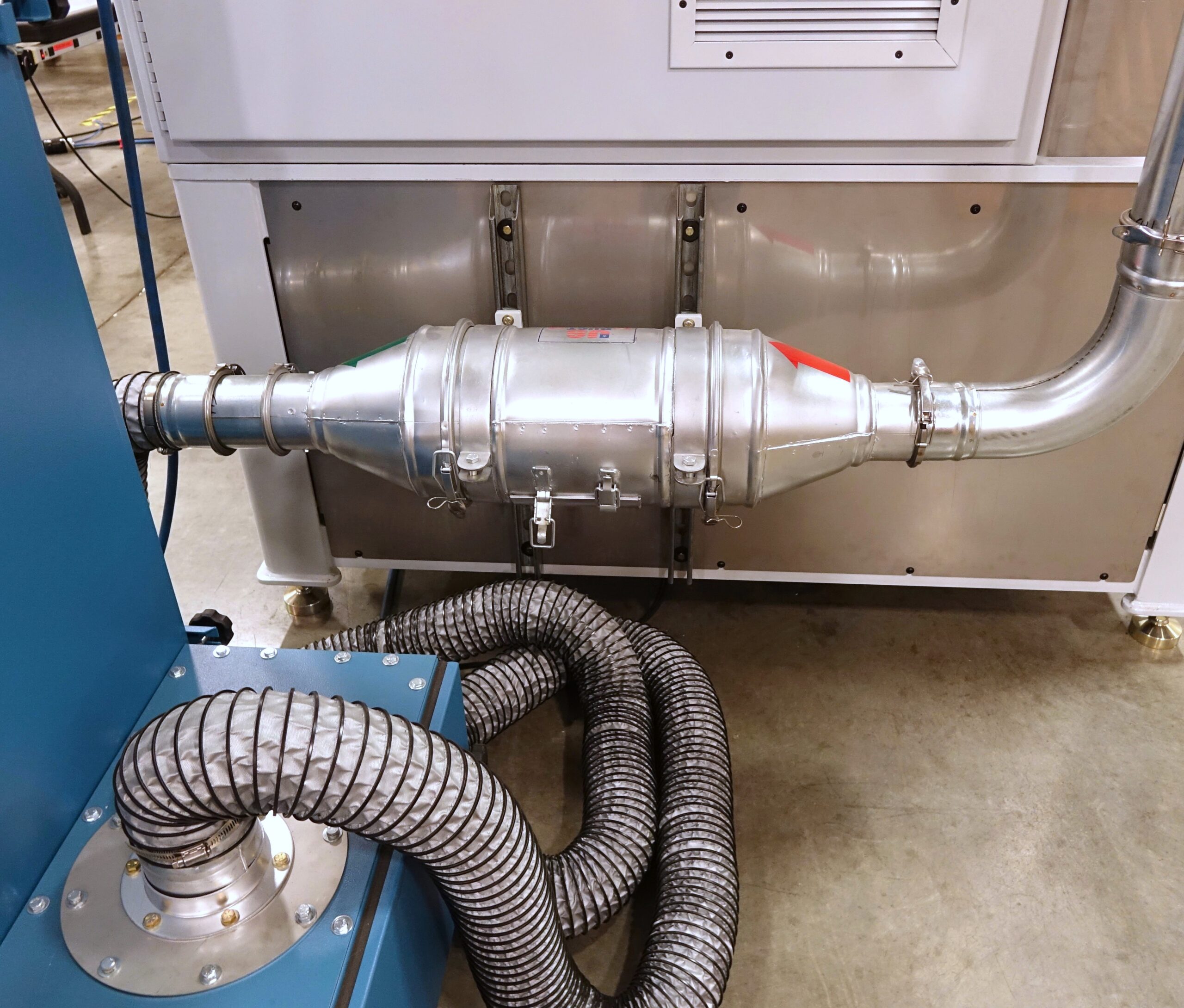
Air Ventilation
Industrial lasers operate reliably and at peak performance in clean environments free from contaminants; for example, condensation or other particles can damage laser optics almost instantaneously when illuminated by a high power laser. Additionally, some laser processes can produce harmful fumes (e.g. welding or marking of certain materials). Thus, ventilation is especially important but can be challenging to implement when the laser is enclosed in a light-tight container. With some creative thinking, AMS has overcome this challenge in a number of ways.
For smaller, simpler applications like laser marking, the enclosure may only need forced ventilation to remain clean and contaminant-free. Anticipating frequent replacement of air filters and the possibility of human error (resulting in the absence of filters entirely), AMS has designed ventilation systems such that filters can be located on the outside of the enclosure while permanent interior light-blocking baffles satisfy the light-tight requirement for reclassifying as a Class I laser system. More powerful laser applications such as welding often generate harmful fumes that can escape when the access doors are opened, potentially exposing operators to hazards. In these instances, AMS has integrated robust fume extraction systems to clean the air and keep operators safe.
Operability and Maintainability
Of course, laser containment and safety are the highest priority when considering reclassification. However, our engineers pay close attention to how this can affect other qualities our customers require and expect such as operability, good ergonomics, and maintainability.
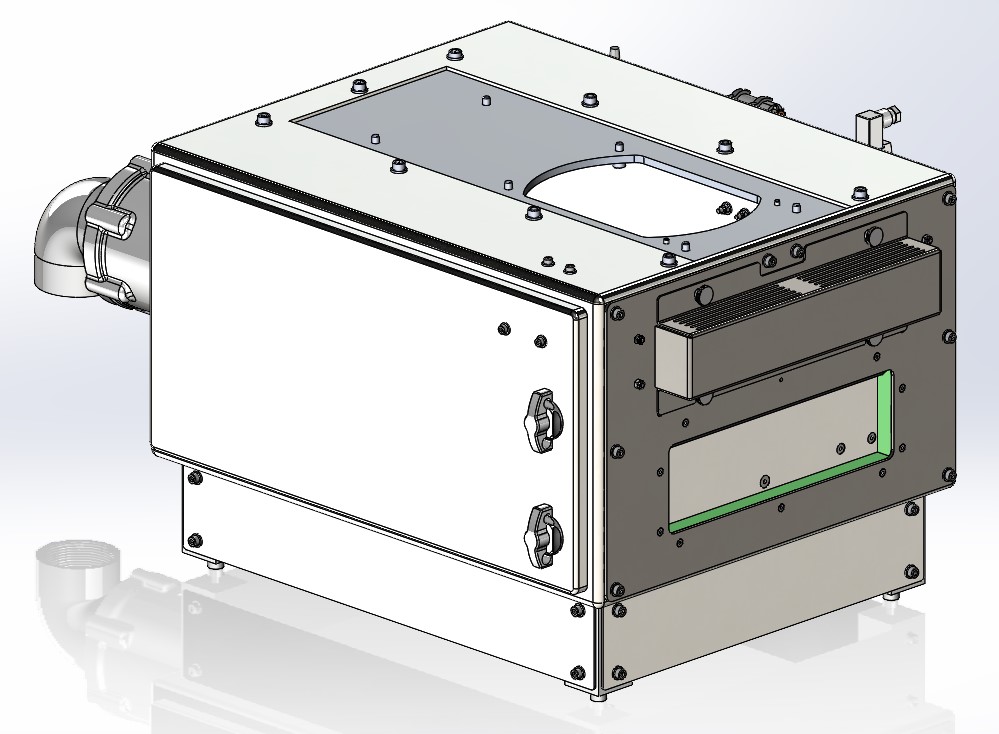
Without introducing needless complexity, AMS laser machines limit the components located within the enclosure to only those necessary for the process. They also include multiple manual access points into the laser enclosure so operators can clear part jams, replace components, and perform regular service. As with automatic doors used in operation, manual doors are monitored by safety interlocks that inhibit laser output when they are open.
conclusion
It is not a trivial task to deploy a Class IV laser – powerful enough to cut, weld, or mark materials – in a safe, Class I system while maintaining required levels of performance. Accomplishing this requires in-depth knowledge of applicable standards and regulations and the ability to solve unique design challenges. Whether it’s finding a way to present parts to the laser, or supplying clean, dry air to the process, or incorporating features that increase accessibility and serviceability, AMS has the aptitude for leading customers through this engineering obstacle course.
*Occupational Safety and Health Administration (OSHA), National Fire Protection Association (NFPA), Federal Aviation Administration (FAA), American Conference of Governmental Industrial Hygienists (ACGIH), and the International Commission on Non-ionizing Radiation Protection (ICNIRP)
start the conversation
All of our collaborations begin with an open dialogue.
Get in touch with us using this simple form, and a member of our team will follow up with you soon.