As a long time supplier to the glass container manufacturing industry, Applied Motion Systems was invited to collaborate with a premier glass container supplier to develop an innovative system to manage the critical task of cooling Individual Section (IS) Machine molds during glass container forming. This system has become the foundation of a flexible and scalable SCADA framework that enables this customer to take its first steps toward plant digitalization and manufacturing adaptability.
Since the deployment of the original pilot project, AMS has incorporated key customer insights to refine and integrate additional systems, providing precise and adaptive mold cooling control that frees up operators. At the same time, plant data is aggregated and analyzed, informing the optimization of production and maintenance operations in plants across North America.
Background
Glass container forming begins with molten glass that is conditioned and delivered to a forming machine where it is metered through an orifice, cut into “gobs”, and distributed to individual section molds within the machine. As the metal molds repeatedly close around the molten glass to cool it and form the final shape of the container, the molds become extremely hot and must be cooled with air supplied by a large fan and duct system. Traditionally, such systems are comprised of adjustable dampers and one or more constant speed fans.
Problem and Scope
A key drawback with legacy cooling system designs is the need for constant manual adjustment of dampers and fans by operators which invariably leads to variable glass container quality and reduced production yield. The glass container manufacturer hoped that by partnering with Applied Motion Systems they would be able to accomplish the following goals:
- Standardize mold cooling systems across plants using a single, large fan configuration with greater capacity to accommodate increasingly variable production demands.
- Incorporate Variable Frequency Drives (VFD) to improve energy efficiency and extend the lifetime of fan motors and fan assemblies.
- Monitor vibration and temperature of fan assembly bearings for early detection of problems and smart scheduling of preventative maintenance.
- Achieve tight, closed loop cooling functionality using an electrically operated Inlet Guide Vane (IGV), fan motor VFD, and feedback from several sensors monitoring key process conditions.
- Incorporate mold cooling control as part of a broader, distributed Supervisory Control and Data Acquisition (SCADA) system with the capacity to include hundreds of sensors across the plant.
- Develop a flexible and scalable solution able to adapt to future requirements.
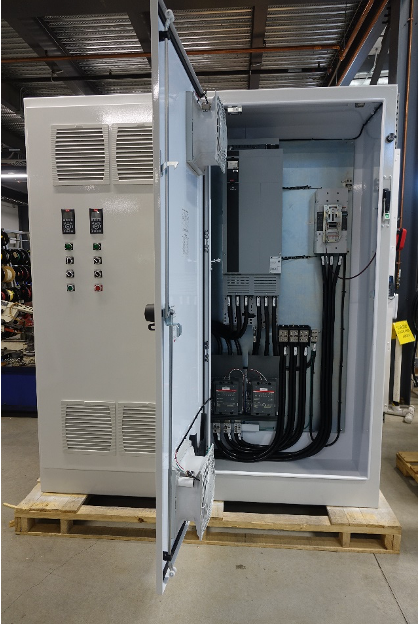
Drive cabinet with redundant 450HP VFD's
System hardware
The Mold Cooling and Plant Monitoring System that resulted from this endeavor performs a multitude of functions. Most importantly, the system controls both fan motor speed and IGV position to achieve fully automated, closed loop control of the mold cooling air at the forming machine. The fan motor is powered by one of two redundant 450hp VFDs and mounted on a fan skid designed with external pillow block bearings for radial fan loading. Using 2‐in‐1 vibration and temperature sensors, each bearing is monitored and vibration evaluated in X, Y, and Z directions, giving plant personnel advance notice of potential mechanical failures. The combination of bearing condition monitoring with redundant VFDs ensures that the system is capable of world class reliability allowing continuous operation while necessary maintenance is conducted during scheduled downtime.
Also, an Inlet Guide Vane damper mechanism is located at the air inlet of the fan assembly and driven by a rotary actuator, controlling position and inlet air flow from fully blocked to unrestricted wide open. Together, the fan motor and IGV comprise the essential mechanical components required for flexible mold cooling, but what makes the system truly effective is the method of control behind these mechanical devices.
adaptive mold cooling
At the center of the Mold Cooling and Plant Monitoring System is a distributed control architecture based on Rockwell Automation technology. This system monitors hundreds of inputs from field devices, sensors, and other systems, many of which are routed to remote I/O collection points in harsh, high temperature, high humidity environments. Feedback from these sources – such as air duct temperature and pressure, ambient air conditions, and IS machine status – is used when calculating system response to mold cooling demands.
The system consistently regulates cooling air to meet these demands during fluctuating ambient conditions (e.g. time of the day, season of the year) as well as automatically compensating for individual sections being shut down for mold swaps or other servicing, all without operator intervention.
The system also recognizes instances when little to no air is required at the IS machine – such as when IS machine parts are being changed out for a different production job – and transitions the system into a low energy standby state. Then, the system automatically resumes regular operation when downtime conditions are cleared, adjusting both VFD and IGV command setpoints to deliver optimum cooling capacity.
Plant SCADA System
Multiple instances of InduSoft Web Studio software on industrial PCs interface with the Rockwell control technology to form a distributed SCADA architecture. The Plant Monitoring System is not simply a user interface for the mold cooling process, rather it is a comprehensive solution that takes the customer one step further into the digital future of manufacturing. It offers key runtime features like trending, alarming, email notifications, reporting – even an in‐context help system for on‐demand training.
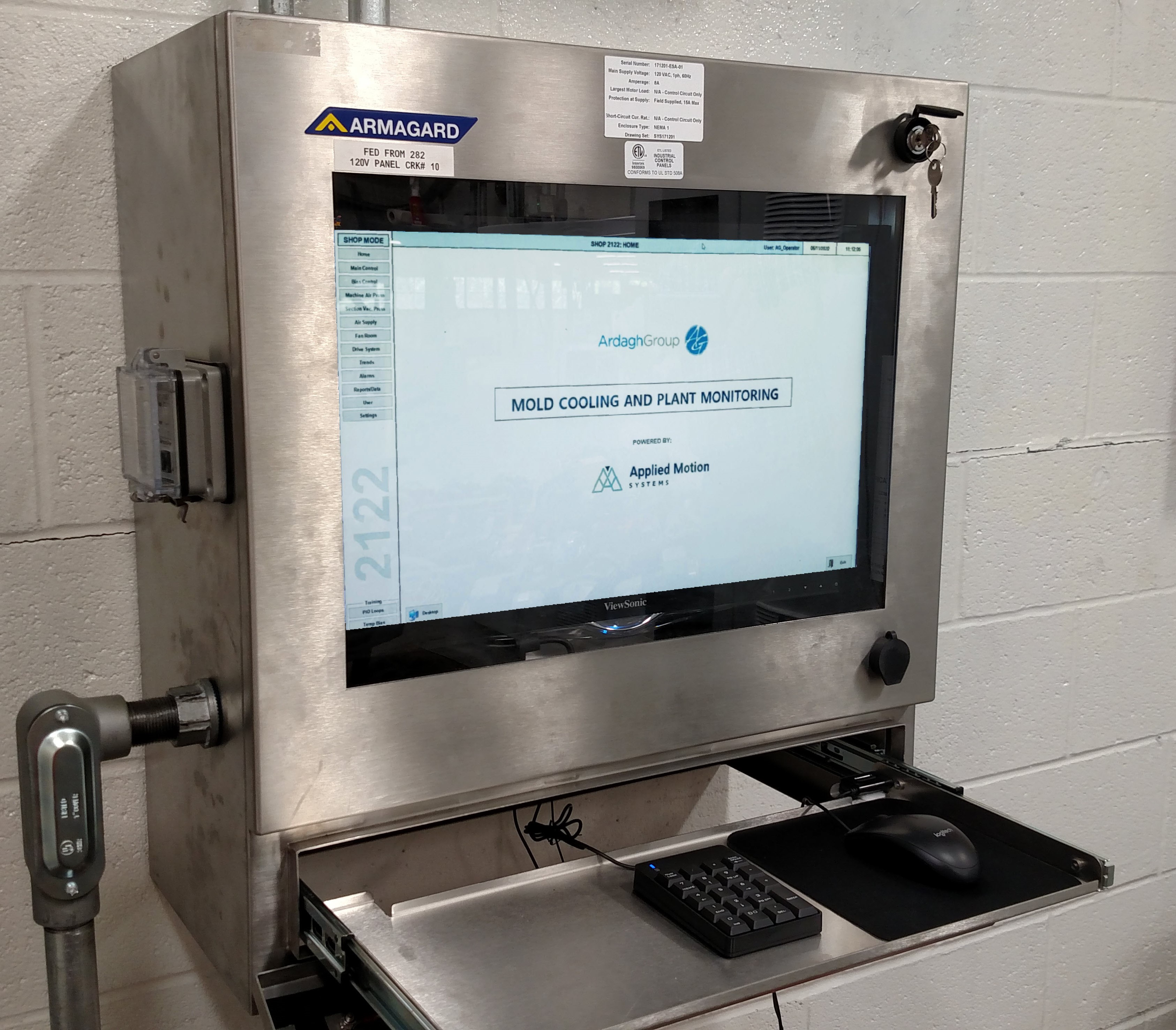
One of multiple operator terminals for SCADA system access
The InduSoft system also offers many benefits characteristic of distributed SCADA systems, such as redundant databases for reliable historical logging, local and remote HMI terminals, hot/standby PC redundancy, and secure, remote web client access by authorized users from anywhere on the network, from plant supervisors to corporate managers. All these features ensure the customer always stays well informed and in control.
With granted network access by the customer, remote support at the SCADA level is simple, easy, and secure. In special cases, a cellular remote support unit can be used to access the local, private control network to troubleshoot components like PLCs and VFDs. These secure lines of communication prove to be highly beneficial for plant personnel who can request remote support from AMS at any time to provide real‐time feedback on system health and functional state. Collaborating in this way, key information is quickly shared between AMS and the customer, enabling timely resolution of issues while simultaneously building a mutual understanding of the system, how it is used, and how it can be improved.
Conclusion
No two Mold Cooling and Plant Monitoring Systems are exactly alike which means flexibility and scalability are essential. Based on Rockwell Automation and InduSoft SCADA technologies, the system has easily grown to meet increasing demands such as integration of water flow measurement using I‐O Link or network data exchange between other AMS or third-party plant systems. With every deployment, existing features are improved, new features are added, and new concepts are developed through close collaboration between customer and supplier. AMS is proud to participate in this fashion, working alongside customers in the glass container manufacturing industry and offering tailored solutions to their growing production demands.